In Stradivari's footsteps
Varnish affects the sound of a violin
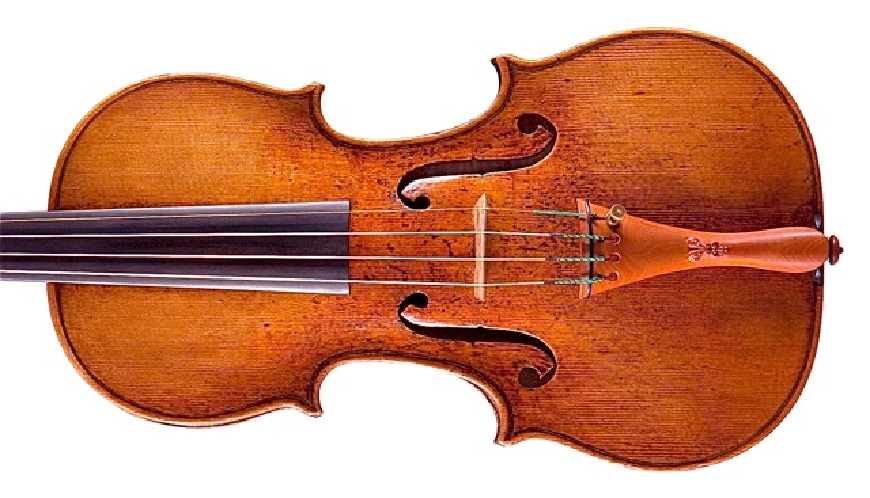
Leonardo da Vinci's oil painting "Mona Lisa" looks rather gloomy with its dark green and brown colours. It is a little-known fact that the maestro painted the picture in bright colours – so the subject appears bathed in the light of a sunny day. What caused this difference in colour? Da Vinci covered his oil painting with varnish to protect it. The varnish acts like a filter, causing the picture to become darker than the artist originally painted it.
It has the same effect on the spruce used to make violins and other stringed instruments. In its raw state, it is white with a touch of gold. The wood lacks durability, so violin makers protect it from environmental damage using a varnish. It is this protective coating that gives the violin its elegant dark brown colour.
Violin makers pass their varnish recipes down from one generation to the next. It is rare for anyone outside the family to find out how exactly the mixture of resins and oils is formulated. The chemistry of varnishes has been scientifically researched for a long time. In contrast, little attention has been paid to the physical properties of varnishes – wrongly in the opinion of Marjan Gilani from Empa's Applied Wood Research Laboratory. The scientist and her colleagues suspected that varnish affects the vibrational properties and therefore the sound characteristics of violins, and they began to investigate this relationship. The first stage of the research was concluded with the publication of a scientific paper in the journal "Applied Physics A". The findings support the Empa researchers' hypothesis.
Four varnishes, 60 wood samples, eleven hours of UV irradiation and conclusive results
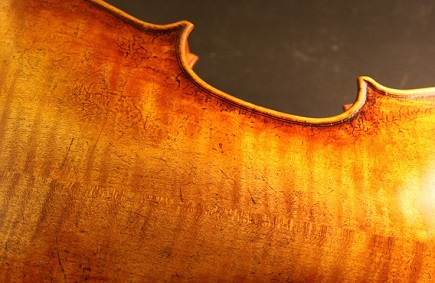
For their research, Gilani and her team cut 40 wood samples in the direction of the grain. 20 of these samples were taken from the young wood and the other 20 from the heartwood of a Norway spruce. Gilani and her colleagues also cut a further 20 samples from the same spruce across the grain. Based on these three types of test samples, the researchers were able to study the sound behaviour of different wood structures. Johanna Pflaum, a trained violin maker, student of environmental sciences and member of Gilani's research group, created two varnishes in the lab. The research group also received two further varnishes from German violin makers. Gilani coated the spruce samples with these four varnishes. For each type of sample, five of the twenty pieces of wood were coated with the same varnish and were dried and cured for eleven hours using UV light.
However before this, the researchers measured the stiffness and sound insulation of the wood samples in their raw state and the mass of the varnish. The purpose of the measurements was to allow the properties of the bare wood to be compared with those of the treated wood. After curing, the experts measured the same parameters again. They also ascertained the sound propagation of the samples at the start and end of the eleven-hour UV irradiation process. Sound propagation describes the way in which tones leave the body of the violin and move towards the audience. Higher sound propagation values result in clearer tones.
In the 40 samples in total that were cut along the grain, the varnish increased the sound insulation of the heartwood and young wood and reduced its stiffness compared to the raw state. This may be desirable because, up to a certain point, the more elastic the wood of the violin, the warmer and softer the sound, particularly in the case of high notes, which can sometimes be perceived as unpleasant. However, this change is accompanied by a loss of clarity and sharpness of the violin sound, which was evident in the laboratory as a reduction in sound propagation. The findings were different for the samples cut across the grain. With these, both the sound insulation and the stiffness increased. Similarly, the sound propagation values also increased. An audience in a concert hall would therefore perceive clear, sharp sounds with strong acoustic presence if the instrument was made in the same way as the samples cut across the grain.Results of X-ray tomography
The wood researchers also analysed part of the samples cut along the grain at the Empa Center for X-ray Analytics. They discerned from the X-ray images that the varnishes formed layers of different thicknesses on the wood and had different effects on the density of the pieces of wood. In addition, some varnishes penetrated deeper into the wood than others. The samples with the highest penetration had been treated with the varnish with the highest oil content. They were also the wood samples that experienced the largest drop in sound propagation – i.e. their tone lost the most clarity due to the varnish.
Following on from these measurement results, a relationship was established between the varnish composition, the microstructure of the wood/varnish composites, their mechanical properties and their sound behaviour. Gilani and her research group intend to refine these findings in other studies. An additional scientist is joining the research team in April 2016 to assist with this work.
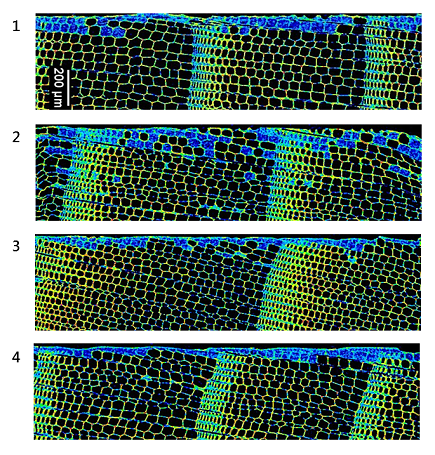
Antique violins at the Empa Center for X-ray Analytics
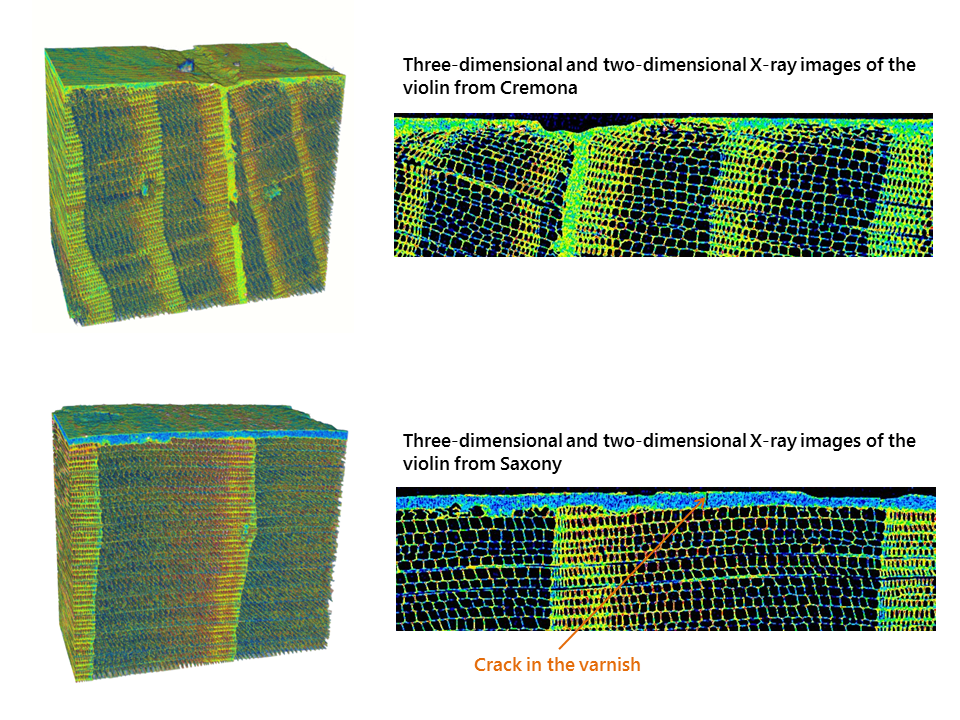
The following animations show the microstructure of both antique violines:
-
Share