Akustik aus dem 3D-Drucker
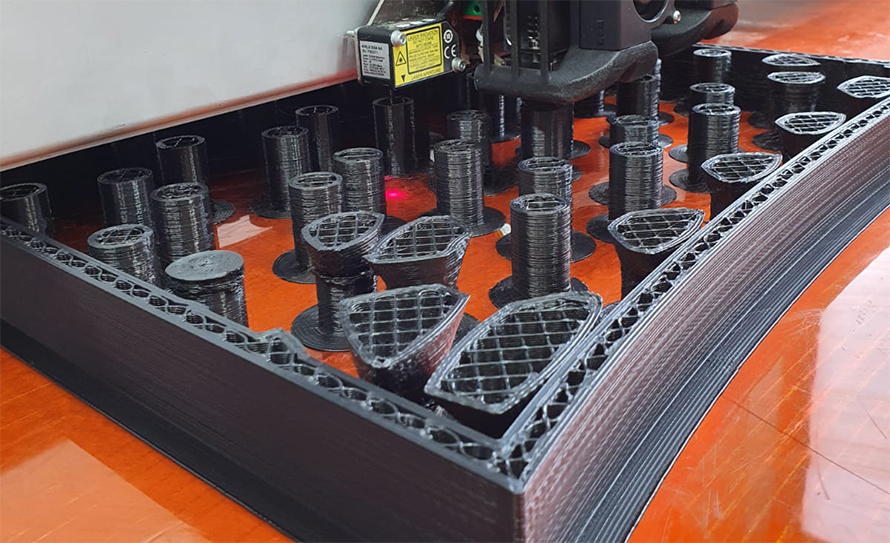
-
Herkömmliche Akustiklösungen stellen oft eine Hürde für die architektonische Gestaltung dar und können die erfolgreiche Umsetzung des Energiekonzepts behindern.
-
Im Deckenprojekt der STEP2-Unit entwickelte das Team eine neuartige Akustiklösung, die dezent in die Filigrandecke integriert wird: Eine Box aus dem 3D-Drucker.
-
Die Innovation ermöglicht eine hohe Akustikqualität eines Raumes trotz schallharter Oberfläche und erweitert gleichzeitig die Gestaltungsfreiheit für die Architektinnen und Architekten.
Im STEP2-Projekt innovieren Partner aus unterschiedlichen Bereichen und Industrien gemeinsam auf Augenhöhe. Daraus gehen schliesslich Innovationen hervor, die auf dem Markt bestehen können. Das Deckenprojekt der STEP2-Unit trägt nun bereits die ersten Früchte dieser Zusammenarbeit: eine 3D-gedruckte Akustikbox, die in die Filigrandecke integriert wird.
Akustik unterstützt Energiekonzept
Ein zentrales Element von STEP2 ist die Optimierung der Energieeffizienz und Behaglichkeit für die Nutzerinnen und Nutzer der Unit. Aus diesem Grund hat die WaltGalmarini AG ein umfassendes Energiekonzept für STEP2 ausgearbeitet. Ein wichtiger Bestandteil davon ist die Sichtbetondecke, die als Speichermasse genutzt werden kann. «Im Laufe des Deckenprojekts wurde für uns klar, dass herkömmliche Akustiklösungen wie beispielsweise Deckensegel die optimale Umsetzung unseres Energiekonzepts behindern würden. Wir mussten deshalb eine Alternative finden», meint Wolfram Kübler, Mitglied der Geschäftsleitung der WaltGalmarini AG.
Die Idee für eine mögliche Lösung entwickelte Silvan Oesterle vom Architekturbüro ROK. Er erstellte eine erste 3D-Skizze für eine innovative Akustikbox, die in die Decke integriert werden kann. Gemeinsam mit den 3D-Druckspezialisten von BASF 3D Printing Solutions, der Stahlton Bauteile AG als Produzent von vorgefertigten innovativen Betonelementen und den Akustikexperten der Empa wurde die Box weiterentwickelt. Das Team konnte aufgrund der Möglichkeiten des 3D-Drucks die Geometrie und Performance weiter optimieren, sodass sich die Akustikeigenschaften sowie auch die Platzierung im Deckenelement nochmals verbesserten.
Dezente Integration
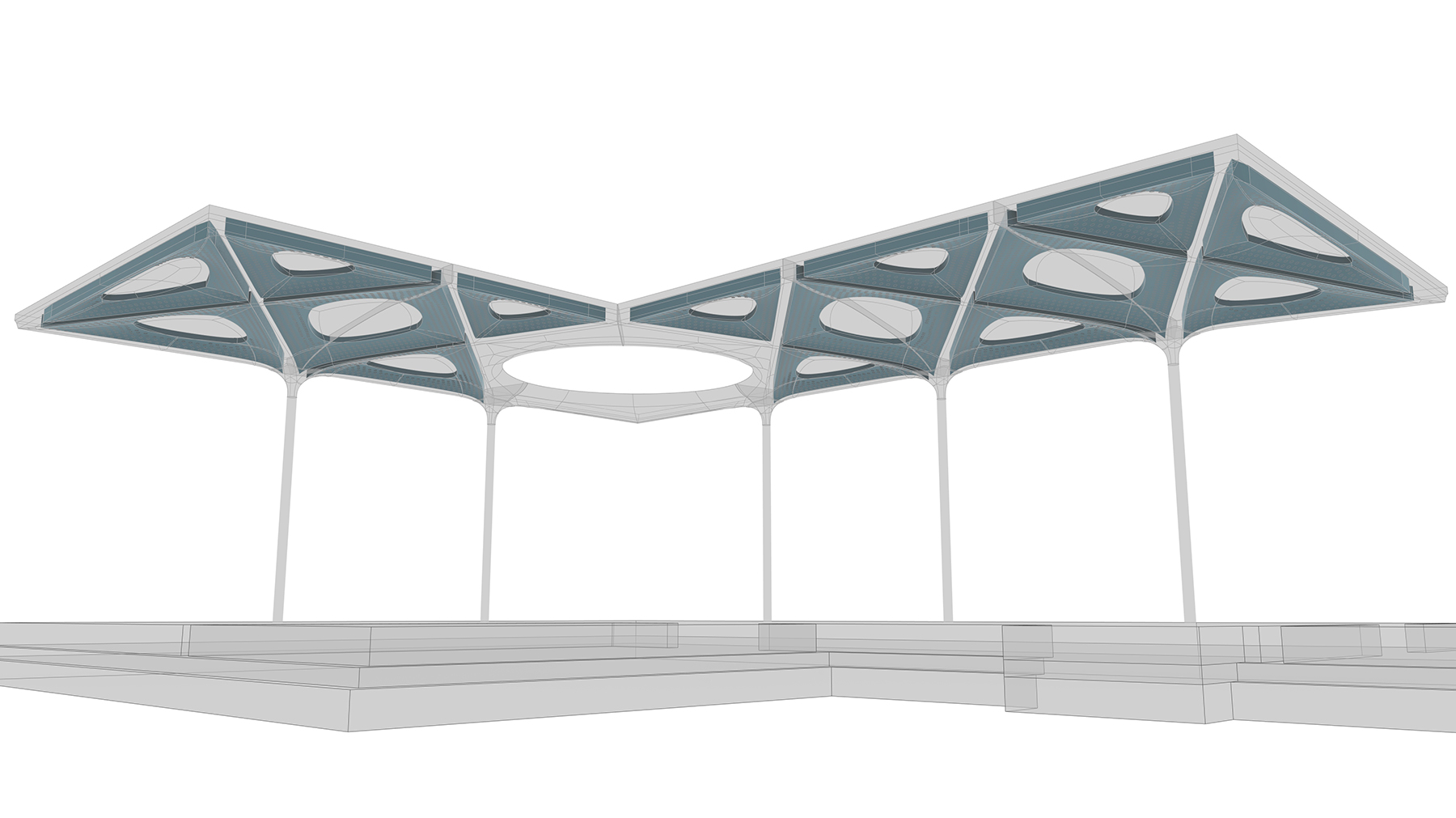
Das Ergebnis der Planung war eine in sich geschlossene Akustikbox, die komplett mittels 3D-Druck hergestellt wird. Das Innenleben besteht aus einem neuartigen mineralischen Absorber-Schaum von BASF, welcher im mittleren Frequenzbereich eine bessere Schallabsorption aufweist als herkömmliche Schallabsorber. Auf der oberen Seite befinden sich Löcher, die den Übergang zur Decke darstellen. Dadurch entsteht in den Deckenelementen eine Perforation, über die der Schall aufgenommen und absorbiert wird.
«Unsere Akustikbox hilft nicht nur dabei, das Energiekonzept wie geplant umzusetzen, sondern sie birgt auch weitere marktrelevante Vorteile», ist Silvan Oesterle überzeugt. «Durch diese Lösung kann die Akustik sehr dezent in die Decke integriert werden. Die Position und Form der Löcher sind zudem variabel, wodurch die architektonische Gestaltungsfreiheit im Vergleich zu herkömmlichen Akustikelementen extrem erhöht wird.» Was auf dem Papier gut klingt, soll in STEP2 in die Praxis überführt werden.
Drucken und giessen
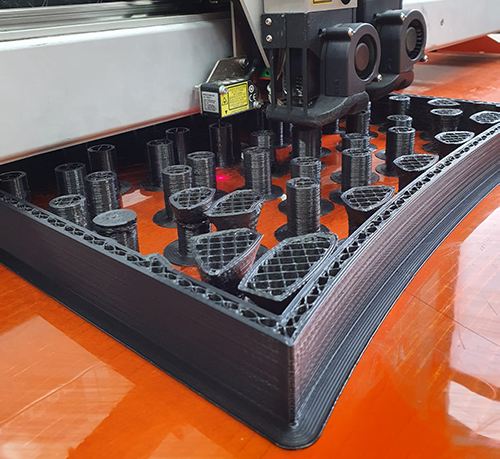
Die Produktion beginnt mit dem 3D-Druck der Akustikbox durch BASF 3D Printing Solutions. Die Geometrie der Box trägt mit einer flachen Unterseite dem Fertigungsverfahren Rechnung. Dadurch ist eine gute Adhäsion auf dem Druckbett ohne zusätzliche Fixierung gewährleistet. Die Produktion wird damit einfacher und kostengünstiger. Bereits der erste Druck lieferte das gewünschte Ergebnis - es waren keine weiteren Iterationen nötig. Für Jörg Petri, Business Development Manager bei BASF 3D Printing Solutions, liegen die Vorteile dieses Herstellungsverfahrens auf der Hand: «Der 3D-Druck bietet die Möglichkeit, eine komplexe Akustiklösung genauso herzustellen, wie sie im 3D Modell geplant wurde. In anderer Herstellungsweise ist die Anpassung an die individuell auftretenden Krümmungen der Decke nicht möglich. Die Akustikbox kann somit mittels der additiven Fertigung einfach und effizient immer wieder neu den jeweiligen Vorgaben angepasst werden.» Für den nächsten Produktionsschritt wurde die Box zur Stahlton Bauteile AG geliefert.
Im Werk angekommen, ging es nun darum, die Lösung in das Beton-Deckenelement zu integrieren. Dies geschieht mithilfe einer individuellen Gussform, in welche die Akustikbox integriert wird. Auch diese Form wird im endgültigen Produktionsverfahren mittels 3D-Drucktechnologie gefertigt. Bei diesem Produktionsschritt ist aufgrund hoher Präzisionsanforderungen die Fertigungskompetenz der Stahlton Bauteile AG gefragt. Die komplexe Geometrie der Akustikbox muss durch einen sauberen Betonguss umschlossen werden. Zusätzlich muss die Sichtbetonseite perfekt mit den Schallröhren der Box abschliessen. Dadurch entstehen schliesslich die Akustiklöcher in der Decke. «Dieses Verfahren führt dazu, dass keine Nachbearbeitung des Deckelements mehr nötig ist. Das stellt eine simple und effiziente Lösung für die Integration der Akustik dar», erklärt Samuel Suter, Leiter Technik und Entwicklung bei Stahlton. Auch hier gelang bereits der erste Versuch. Der Betonguss war fehlerfrei und die Qualität der Sichtbetonseite mit den Akustiklöchern übertraf sogar die Erwartungen des Projektteams.
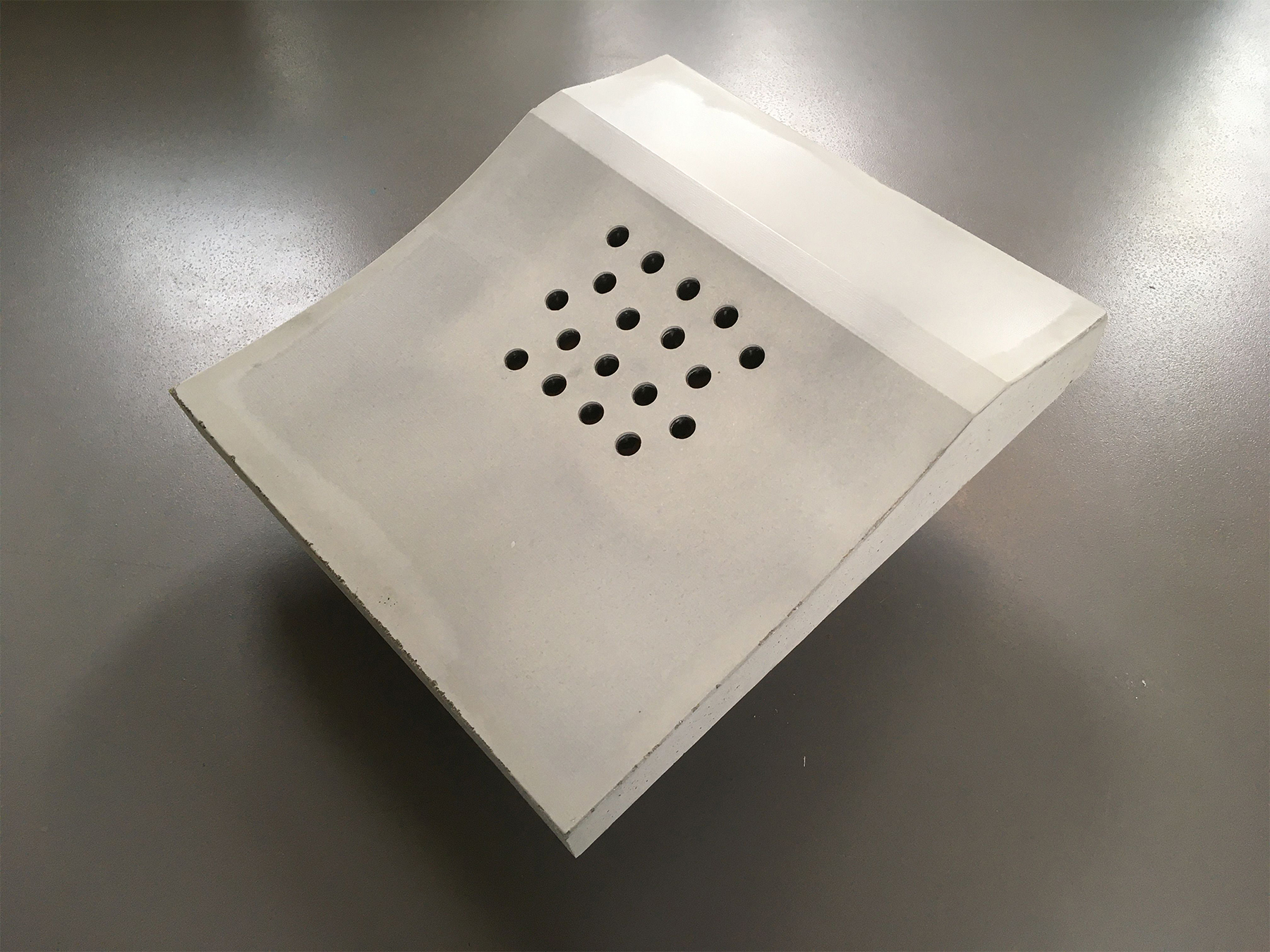
Überzeugendes Konzept
Das Projektteam zeigte sich zufrieden mit dem ersten Ergebnis. Mit dem Prototyp konnte nachgewiesen werden, dass das ausgearbeitete Konzept funktioniert und hohes Potenzial birgt. Die innovative Akustikbox bietet die Möglichkeit, eine hohe Qualität bei der Akustik eines Raumes trotz schallharter Oberfläche zu erreichen. Gleichzeitig kann die Sichtbeton-Decke weiterhin als Speichermasse aktiviert werden.
Im nächsten Schritt wird das Team das Herstellungsverfahren weiter optimieren. Eine wichtige Frage wird dabei sein, wie sich die Integration der Box in Recyclingbeton verhält. Falls der zweite Prototyp mit diesem Beton gelingt, soll im Herbst ein erster grösserer Ausschnitt des gesamten Deckensystems erstellt werden.