Cooperative project between Technical Universities and Industry
Empa clears the way for lead-free solder
In three years time, the ban on the use of use of lead in electronic solder will come into force. To meet this ban, new production processes in the electronics manufacturing industry are required. A major question is which alloys are suitable as environmentally friendly lead-free alternatives to current solders. EMPA researchers have encapsulated their expertise on modified production techniques and presented their recommendations in a one-day symposium for industry held on the 28th March at the EMPA Academy.
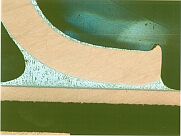
In the electrical and electronic industries, soldering with lead-containing solder is currently one of the most important interconnection techniques. However, the new European regulations, which will take force in 2006, have sounded the death-knell for lead-containing materials. Lead is a particularly problematic toxin due to its tendency to accumulate in organisms along the length of the food chain (bio-accumulation) and because of its persistence. The emission of lead and its derivatives into the environment must therefore be reduced drastically |
||||
Much experience with lead-free soldering In the Eureka project “Leadfree” the EMPA, the Fraunhofer Institute ISIT, Itzehoe, Germany, the Technical University, Vienna and various European industrial partners* have been investigating alternative, lead-free solders. While there are a number of such solders already on the market, there is a lack of easily accessible, accurate information on the associated production and reliability issues. The use of lead-free solder demands modifications to production processes because, for example, lead-free solders have higher melting points than traditional lead-tin alloys. The old production processes must therefore be adapted to suit the new conditions in a transition phase. The industry is very interested in this information, since data on (ideal) production methods is literally worth its weight in gold, and also eliminates the need to perform in-house research. |
||||
|
Tin-silver-copper alloy is favorite The development of lead-free soldering techniques is a tricky business. It is not just the increased temperature, which causes production difficulties. Components and printed circuit boards must not be damaged during the soldering process. For test purposes the product team therefore had 1100 boards manufactured with tin-lead, nickel-gold and chemically deposited zinc surfaces. This then allowed a range of potentially useful alloys to be identified, of which tin-silver-copper (SnAgCu) emerged as the material of first choice. Production tests have demonstrated that using this alloy permits similar soldering conditions to be used to those employed today. There is therefore no need for dramatic changes to the manufacturing process. * Swiss industrial partners are Elcoteq AG Turgi, Oerlikon Contraves, Schindler Electronics, Siemens Building Technologies, Siemens (Schweiz) AG and Ascom. |
|||
For further information: Electronics/Metrology Laboratory: Günter Grossmann, Phone +41-1-823 42 79 Dr. Urs Sennhauser, Phone +41-1-823 41 73 |
||||
|
||||