Selective Laser Melting
Selective Laser Melting (SLM) is a well established AM technology to produce metal parts. In the SLM process, metal powder is melted by the energy of a laser beam. The part is built layer by layer. After the laser has melted one layer a new layer of powder is added to the resulting work piece. Then the laser is used again and melts the next layer.
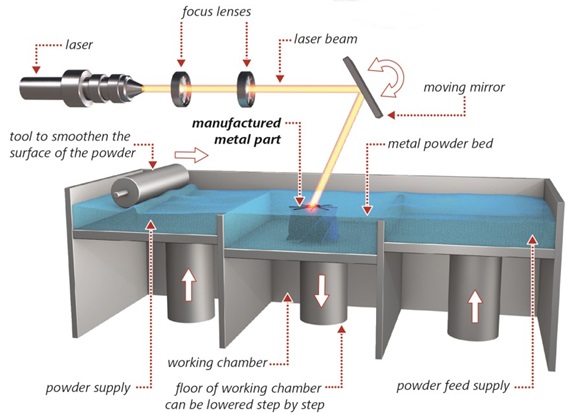
Processing characteristics
The key characteristics of the SLM process can affect the material selection, the component design and the final application:
- High cooling rates in the range of 10'000 – 100'000 °C/s can lead to problems with the processing of conventional alloys, but allow also to achieve novel microstructures and to process novel alloy compositions.
- The material must be available as powder with the right grain size and morphology.
- The amount of powder for a build job is determined by the sample height; High components require a large amount of powder
- Several part geometries need additional support structures, which will have to be removed from the part afterwards
Materials
- Commercially availabel : Stainless steel (1.4404), aluminium alloys (AlSi10), titanium alloys (TiAl6V4, Ti Grade 2), Nickel alloys (In 718, In 625), Co-Cr alloys
- Research: Metal-matrix-composites, structural intermetallic alloys, high temperature alloys
SLM Maschines at Empa
Empa operates in the Coating Competence Center two commercially available SLM machines from renowned machine manufacturers:
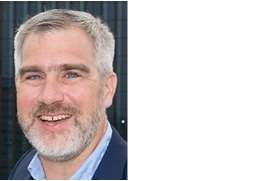
-
Share