Acoustics from the 3D printer
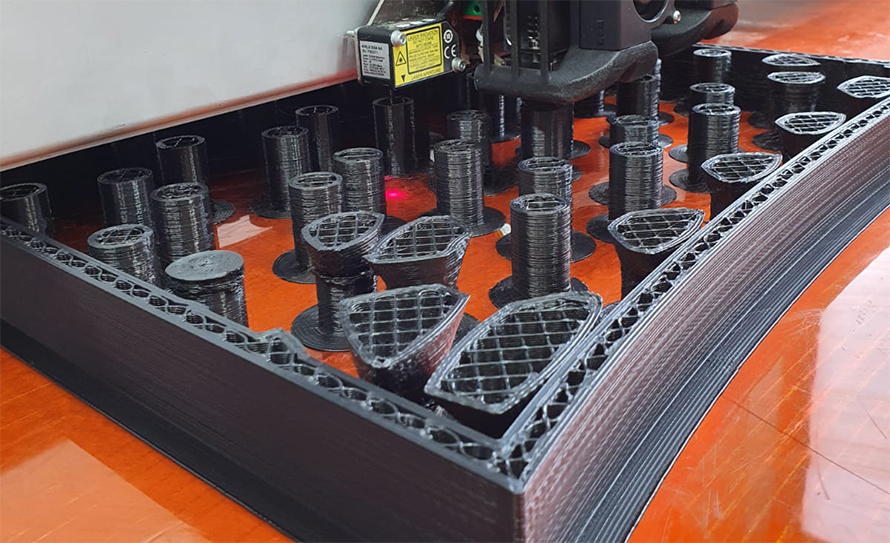
-
Conventional acoustics solutions often pose a hurdle to architectural design and can hinder the successful implementation of energy concepts.
-
In the STEP2 unit's floor slab project, the team developed a novel acoustics solution that will be discreetly integrated into the ribbed filigree slab: A box from the 3D printer.
-
The innovation enables a high acoustics quality of a room despite a sound-reflecting surface and at the same time extends the design freedom for the architects.
In the STEP2 project, partners from different fields and industries are working together in an open innovation approach. This ultimately results in innovations that can succeed on the market. The STEP2 unit's floor slab project is already bearing the first fruits of this collaboration: a 3D-printed acoustic box that is integrated into the filigree slab.
Acoustics support the energy concept
A central element of STEP2 is the optimization of energy efficiency and comfort for the users of the unit. For this reason, WaltGalmarini AG has developed a comprehensive energy concept for STEP2. An important component of this is the exposed concrete slab, which can be used as a storage mass. "During the planning process of the floor slab, we realized that conventional acoustic solutions such as ceiling sails would hinder the optimal implementation of our energy concept. We, therefore, had to find an alternative," says Wolfram Kübler, member of the management team at WaltGalmarini AG.
Silvan Oesterle from ROK Architects developed the idea for a possible solution. He created an initial 3D sketch for an innovative acoustics box that can be integrated directly into the floor slab. Together with the 3D printing specialists from BASF 3D Printing Solutions, Stahlton Bauteile AG as a producer of prefabricated innovative concrete elements and the acoustics experts from Empa, the box was further developed. Thanks to the possibilities of 3D printing, the team was able to further optimize the geometry and performance, so that the acoustics properties and the placement in the floor slab element were further improved.
Discreet integration
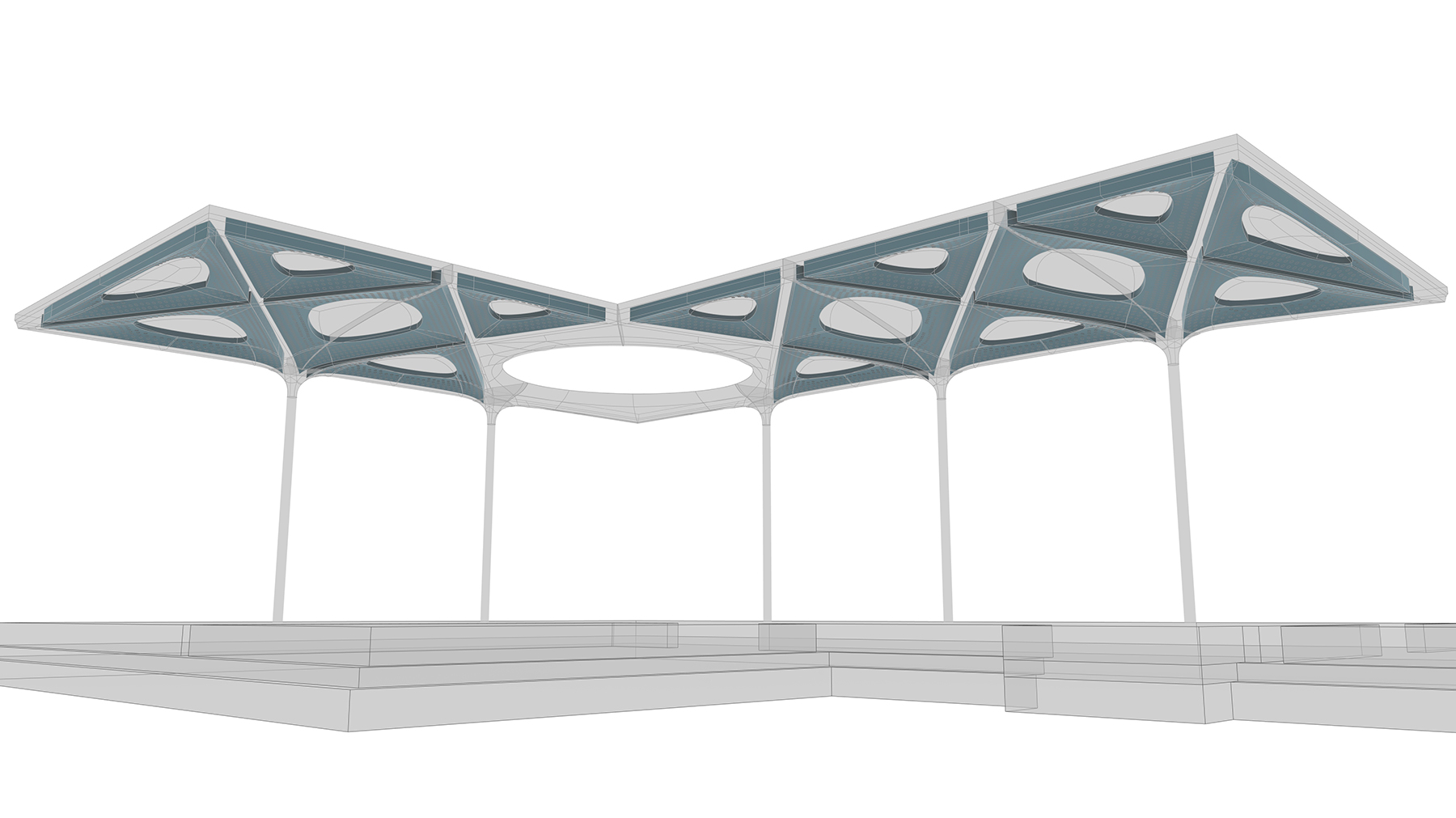
The result of the planning was a self-contained acoustics box that is manufactured entirely by means of 3D printing. The interior consists of a mineral-based insulating material from BASF, which offers better sound absorption in the medium frequency range than conventional sound absorbers. On the upper side of the box, there are holes that form the connection to the floor slab. This creates a perforation in the floor slab elements through which the sound is absorbed.
"Our acoustics box not only helps to implement the energy concept as planned, but it also holds other market-relevant advantages," Silvan Oesterle is convinced. "This solution allows to integrate the acoustics very discreetly into the floor slab. Furthermore, the position and shape of the holes are variable, which extremely increases the architectural design freedom compared to conventional acoustics elements." What sounds reasonable in theory is to be put into practice in STEP2.
Printing and casting
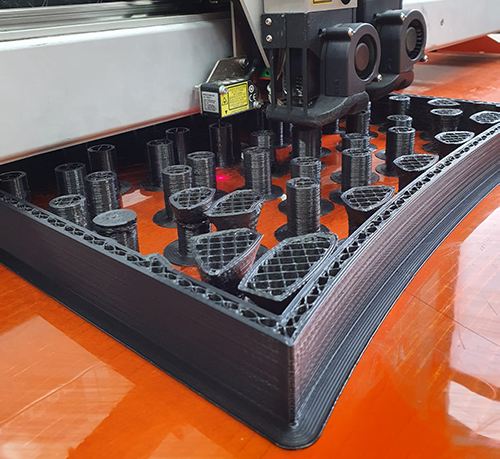
Production begins with the 3D printing of the acoustics box by BASF 3D Printing Solutions. The geometry of the box has a flat underside to meet the requirements of the manufacturing process. This ensures good adhesion to the print bed without additional fixation. The production is thus simpler and more cost-effective. The first print already delivered the desired result – no further iterations were necessary. For Jörg Petri, Business Development Manager at BASF 3D Printing Solutions, the advantages of this manufacturing process are obvious: "3D printing offers the possibility to produce a complex acoustics solution exactly as it was planned in the 3D model. In other manufacturing methods, it is not possible to adapt to the individual curvatures of the floor slab. The acoustics box can therefore be adapted simply and efficiently to the respective specifications each time using additive manufacturing." For the next production step, the box was delivered to Stahlton Bauteile AG.
After arriving at the factory, the next step was the integration of the solution into the concrete floor slab element. This is done by using an individual mold in which the acoustics box is integrated. In the final production process, this mold is also manufactured using 3D printing technology. Due to the high precision requirements, this production step calls for the manufacturing expertise of Stahlton Bauteile AG. The complex geometry of the acoustics box has to be enclosed by a clean concrete casting. In addition, the exposed concrete side must be perfectly sealed with the sound tubes of the box. This ultimately creates acoustics holes in the slab. "This approach means that no post-processing of the floor slab element is required. This is a simple and efficient solution for the integration of the acoustics," explains Samuel Suter, Head of Technology and Development at Stahlton. Again, the first attempt was a success. The concrete casting was flawless and the quality of the exposed concrete side with the acoustics holes even exceeded the expectations of the project team.
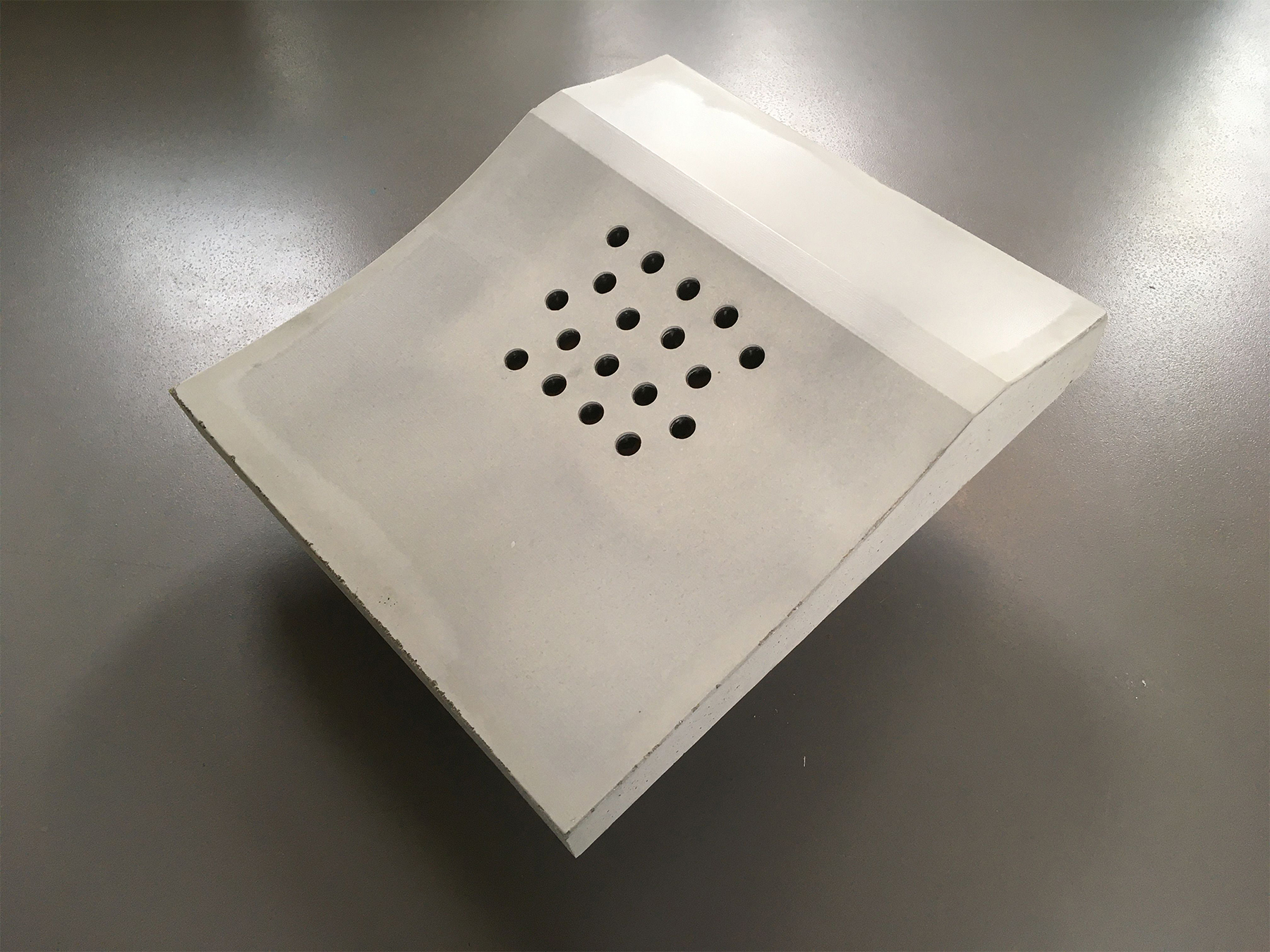
Convincing concept
The project team was satisfied with the initial result. The prototype proved that the elaborated concept works and has high potential. The innovative acoustics box provides the opportunity to achieve high quality in the acoustics of a room despite a sound-reflecting surface. At the same time, the exposed concrete slab can still be used as a storage mass.
In the next step, the team will further optimize the manufacturing process. An important question will be how the integration of the box in recycling concrete behaves. If the second prototype with this concrete is successful, a first larger section of the entire floor slab system will be produced this fall.