Smart ceramic processing
The focal point of the tasks lies in the interdisciplinary collaboration in the production of functional materials and composites. Developing prototypes of fibres, hollow fibers, foils and tubes is the main focus in the process development for developing novel system components.
> An overview of Smart Processing for Ceramics and Sensor-Composite Materials you find here:
Overview-PDF (982KB)
Thermoplastic forming Ceramics
The Laboratory for High Performance Ceramics is engaged in the development of thermoplastic forming and the development of thermoplastic binder systems for pressing, extrusion, injection molding, dip coating and 3D printing of ceramic components. Due to its many years of experience, the group does not focus on a specific binder system, but rather develops and optimizes customer-oriented, individual solutions. In the course of these developments, binder systems for the thermoplastic 3D printing of ceramic powders are also being developed. The additive manufacturing process of thermoplastic composites (Fused Deposition Modeling - FDM or Fused Filament Fabrication - FFF) is a recognized and widespread technology for the production of complex macroscopic structures. Empa develops thermoplastic binder systems, which enable cost-effective printing of ceramic components with conventional (open-source) FDM printers. Figure 1 shows the most important factors that influence the 3D printing of ceramics.
Figure 1: Typical factors influencing thermoplastic 3D printing of ceramic materials
blue = machine factors,
red = material failures
The 3D printing of thermoplastic ceramics offers the possibility to produce components individually via layered deposition. Typically, thermoplastic filaments are fed into a heated nozzle via a Bowden extruder. The polymer binder is melted and deposited in a desired position. After cooling and hardening, a structure with a layer thickness between 0.03 and 1.2 mm can built up.
The process is divided into several production steps:
- Compounding of the ceramic powder and the thermoplastic binder
- Filament or granule production for thermoplastic 3D printing
- 3D printing by melting the filament and layered deposition of the material
- Thermal treatment (debinding and sintering of the components)
Post-treatment of the component surface can be done on the printed, debinded or sintered state. Figure 2 shows a commercially available simple 3D printer used for materials development.
Figure 2: Commercially available 3D printer for the development of thermoplastic ceramic materials.
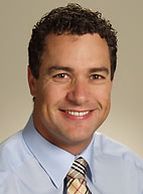
Scientists:
Dr. Arun Ichangi
Dr. Elham Montakhab
PhD-Students:
Christopher Bascucci
Somashree Mondal
Sofiia Butenko