Empa assigns patent rights for textile fiber metallizing process to Swiss company
An innovations impulse for the Swiss textile sector
Metallized fibers are currently at the focus of a lot of attention in the textile industry. At the end of 2007 Empa transferred the rights to its patent for a special fiber coating process to Tersuisse Multifils SA in Emmenbruecke, at the same time handing over its pilot plant to the company. This new technology, developed at Empa, will help strengthen the Swiss economy in the global textile market. The new process allows the fiber coating to be significantly thinner than previously, thus reducing both costs and material consumption while improving environmental friendliness and yet still maintaining the useful characteristics of the finished textile.
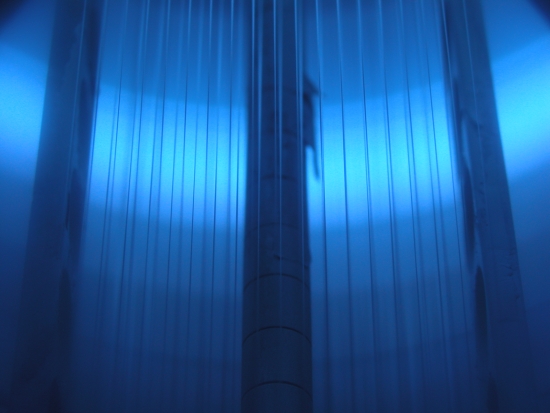
Caption: Textile fibers in the plasma coating plant Silver coated fibers and cloth help protect against bacteria, UV radiation and electrosmog. However, until now the conventional electrochemical-based manufacturing process also produced large quantities of environmentally unfriendly waste water and the quality of the textile itself as a rule suffered under the coating technique too. A sustainable alternative is metallization of the fabric with the help of a low pressure plasma (see box). However this process has to date been quite simply too expensive for use in the textile industry. Now, Empa scientists working together with industry partners have developed a plasma coating plant which is more than competitive. At the end of last year, Empa assigned its patent rights to a Swiss company, Tersuisse Multifils SA in Emmenbruecke, and at the same time passed on its pilot plant, thus helping to strengthen the Swiss textile industry. |
||||
New fiber guidance system makes plasma technology more economic The key to Empa’s success is a new fiber guidance system. On the one hand this allows a more rapid coating process and on the other it leads to the metal being applied more efficiently to yarns and fibers, which reduces the metal consumption. Both factors help to reduce manufacturing costs significantly, ensuring that in comparison to the conventional electrochemical process the advantages of the new technology take center stage. |
||||
|
An additional plus point is that the plasma technique produces no potentially polluting waste products. No less important is the fact that the metal coating applied is ten to twenty times thinner that obtained electrochemically, for the same or even better yarn quality. The finished materials retain their characteristic and desirable textile properties such as processability (i.e. suitability for further working such as weaving and knitting) and still have the same “feel” after coating. The thinner the metallic coating, the better it adheres to the fiber. This means that metal ions do not get washed out of the finished fabrics during cleaning and so do not end up in the waste water system. |
|||
Often all that is missing is the fiber with the “right” properties «One great advantage is that plasma-metallized fibers are coming onto the market just at a time when numerous concrete applications already exist for them. In addition to this, there are other new applications such as portable electronic systems which are in an advanced stage of development. Often all that is missing are fibers with the “right” characteristics,” is how Manfred Heuberger, head of Empa’s Advanced Fibers Laboratory gauges the future innovation potential of the new technique. Currently he and his colleagues are working on plasma coating methods which will “equip” fibers and textiles with completely new characteristics. |
||||
|
The fact that now an established yarn manufacturing company has been found to take over the patent rights and operate the pilot plant has two important consequences; firstly, it makes the immediate manufacture of metallized fibers possible, and secondly it relieves Empa’s partners from the textile processing industry, who worked together with the research institution on the development of the plasma coating process, of the necessity of making large investments in their own fiber production plant. Apart from Empa the project team included Roth & Rau AG (a German plant construction company), Keller AG (a manufacturer of drapes, decorative textiles and functional fabrics based in Wald, Zurich canton), Rotecno AG (a canton Ticino-based producer of clothing for surgical use and for hospital patients) as well as Christian Eschler AG of Buehler, St. Gall canton (a company specializing in knitted fabrics). The project was financially supported with a budget of CHF 2.5 million by the Swiss Innovation Promotion Agency (CTI). | |||
Further information: Editor: |
||||
|
||||
|
||||