Recycling
With a pinch of rubber
Swiss drivers wear out countless tires. Instead of incinerating them, they could be reused locally: The asphalt of various countries has long contained rubber from used tires. Empa and its partners from industry are adopting this idea for potential applications in Switzerland.
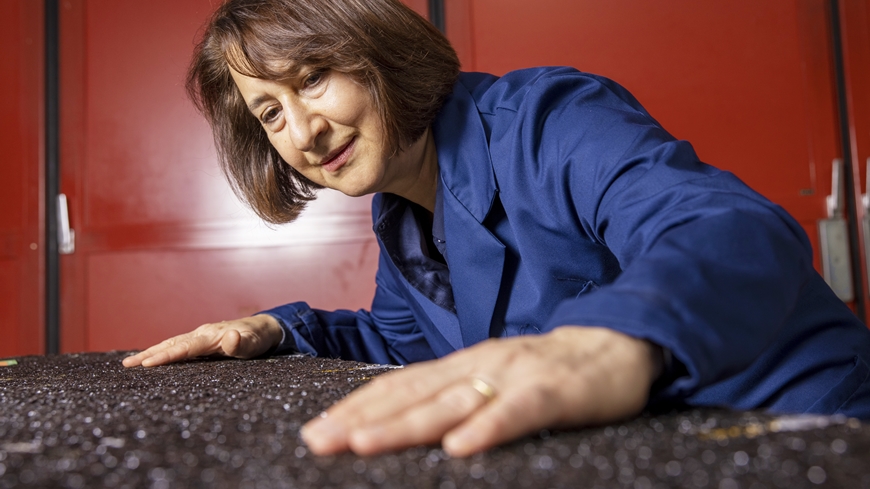
Commuters who nag about traffic stress should look at the ground every now and then. And take comfort in realizing it might be worse, much worse: Asphalt endures blistering heat, cold stress and plenty of pressure from above. It should also be as quiet as possible – and in the future, of course, more environmentally friendly.
Composed from a hot rock mixture and the binder bitumen at around 160 degrees, asphalt causes substantial CO2 emissions – through production, long transport routes and paving. To improve its environmental footprint, old asphalt, which can already be recycled, will be used on a large scale in new pavements in the future. Moreover, recycled concrete or other residual materials – such as used car tires, of which there are plenty in Switzerland – can be "disposed of" in it.
An Innosuisse project led by Empa's Concrete and Asphalt lab has explored what benefits this idea could have in Switzerland. Specifically, can rubber particles replace the polymers in polymer-modified bitumen for heavy-duty asphalt? After all, compounds such as the widely used styrene-butadiene-styrene give pavement more plasticity, better recovery and longer life.
The focus of the project was on the practical implementation of the technology: After some preliminary tests, the asphalt mixtures for the experiments were produced by the manufacturers FBB and Weibel AG. The mix design was based on the standard semi sense asphalt SDA 4-12, a low noise surface course due to its high air void content. The AC B 22 H is a so called binder course that is placed under the surface course – in this case currently with 30 percent recycled asphalt. The selected rubber granules also came from Switzerland, from the manufacturer Tyre Recycling Solutions (TRS) in Préverenges in the canton of Vaud.
Wet or dry?
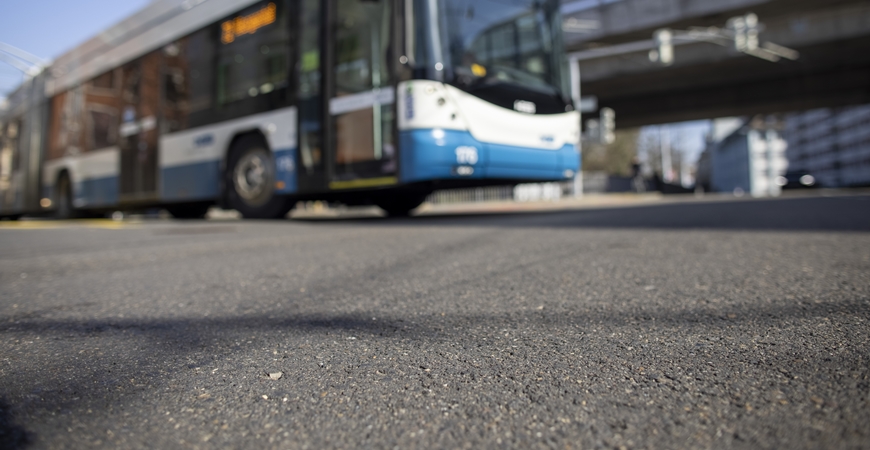
Rubber asphalt can be produced using two different methods. In the "wet" method, the rubber granules are added to the hot bitumen; then the mixture is mixed with the defined aggregate - sand and gravel of different sizes, depending on the pavement. The catch is that the bitumen-rubber mixture becomes less viscous over time and the rubber begins to decompose; it can only be processed for about 48 hours. In the "dry" process, on the other hand, the rubber particles first trickle into the heated aggregate mixture. The bitumen is added later. Because the Swiss manufacturers are prepared for this, this path was chosen.
The experience at building materials manufacturer FBB in Bauma has thus far been positive. "No problem," says Christian Gubler, chairman of the management board, "it was easy." The particles were thrown through a flap into the aggregate mix – in bags that dissolve at high temperatures. "Just like we do when we add colorants, for example, for red asphalt," Gubler explains. There were no difficulties at Bern-based Weibel AG either. "The handling was trouble-free," says Samuel Probst, head of bituminous construction materials and pavement plants.
Stress tests under water, cold and pressure
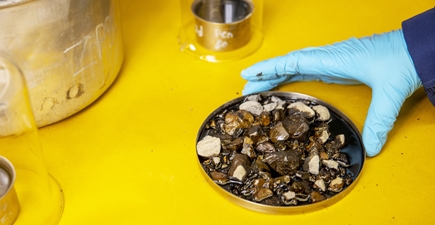
An Empa team led by asphalt specialist Lily Poulikakos examined the final products from micro to large scale. In addition to standard tests for bitumen content and air voids, electron microscope images showed whether and how the rubber particles dissolve and distribute within the asphalt matrix.
In the splitting tensile test, test specimens were burst under pressure from above – one wet and one dry – to determine how sensitive they are to water. Tear tests at minus 12 degrees showed how the material behaves in cold winter conditions. Finally, the traffic factor: In the "Hamburg Wheel Tracking" test, samples in 50-degree hot water endured 10,000 passes of a steel wheel weighing a good 70 kilograms – a tough test for rutting. Empa's own simulator was aimed in the same direction: It subjected 1.20-meter-long linings to 60,000 slow tire runs with high loads over the course of eight hours.
The analyses showed that it's details that matter. For instance, the optimum time between mixing and installation on the road depends heavily on the type and quantity of rubber granulate. In comparison with the well-known polymer bitumen asphalt, the surface course asphalts with 0.7 or 1 percent rubber fulfilled the requirements in the majority of cases. Resistance to cracking due to cold was significantly greater with one percent rubber than with the polymer bitumen asphalt. In terms of water sensitivity, the construction materials met the Swiss requirements, with one exception. And in Empa's own tire load simulator, small but deeper ruts appeared in the rubber asphalts than in the polymer bitumen pavement.
The conclusion: Despite some drawbacks, the rubber asphalt ultimately met the requirements. "It is definitely suitable for further investigations for use in road construction," sums up Empa researcher Poulikakos. Manufacturer TRS is also pleased with the results: "We now have a professional confirmation," says Sonia Megert, Chief Operating Officer. "It was a very good collaboration. Empa quickly found a solution whenever problems arose."
Of course, all partners are aware that this is only the first step. Despite all the efforts, the laboratory does not correspond to real-world conditions, explains Poulikakos. The experiments do give a detailed impression, but how years of exposure will play out in reality "is another matter," says the specialist. "The truth lies ultimately on the road."
Three test routes
Further steps have already taken place. In the cantons of Jura and Vaud, Weibel AG built two test sections on cantonal roads using rubber granulate asphalt. "A rough asphalt on a road with a medium load," explains Samuel Probst, "and a surface asphalt on a road with a relatively high load. After all, they were supposed to be real endurance tests."
Unlike previous experiences with the "wet" production process, the paving went "absolutely smoothly," according to the manager in charge. On site, the workers did not have to endure any odors from heated rubber, and the consistency and workability of the asphalt was comparable to a polymer-modified asphalt. Admittedly, it will only show its true character after years. Paving took place last summer; the pavement is thus still in its infancy.
Just like another test asphalt, which was laid as top layer at a heavily used intersection in Zurich. Its laboratory values were not beyond doubt: When the bitumen was hardness tested with a penetrating needle, the results fluctuated wildly and were sometimes well above the target values. "That suggests it might be too soft," says pavement specialist Martin Horat of the civil engineering office of the city of Zurich. "Let's see if there are deformations when it gets hot in summer."
Hans-Peter Beyeler, director at the "Eurobitume" association in Switzerland, is not particularly worried, though. "I already heard about that. I wouldn't worry about it for the time being," says the expert, who previously worked for almost 13 years as a pavement specialist at the Federal Roads Office (Astra). When rubber and bitumen are mixed, a new material is created; its behavior no longer corresponds to the original ingredients. His assessment: "The needle test may simply not provide useful information."
From his own experience, Beyeler understands that there is also resistance in the industry to asphalt as a "garbage chute" for recycled materials and skepticism about rubber in the road. Some 15 years ago, he witnessed how a test on the A1 in the canton of Aargau with rubber-modified bitumen, added as granules, went thoroughly wrong: The material was insufficiently dissolved in the mix; lumps formed in the asphalt. In the pavement, they spread on the surface; they had to be drilled out and filled with mastic asphalt.
The truth is on the street
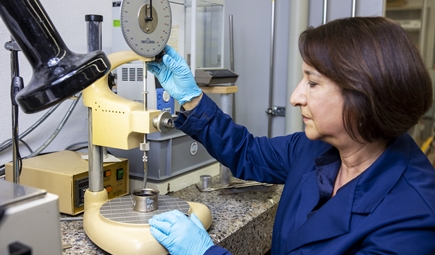
A lot has happened since then, however, so why not try again, Beyeler thinks. After all, there is good experience – not only in the US, where the technology has been in practice for a long time, but also in Bavaria. There, rubber-modified asphalts are already part of the building regulations – in other words, state of the art. The advantages, especially for porous surface courses: higher abrasion resistance, slower oxidation of the bitumen in the many air voids and thus delayed embrittlement. In short: a longer service life.
In any case, there would be enough raw material. Around 70,000 tons of scrap tires are produced in Switzerland every year. A small proportion of this is recycled, but the majority is thermally utilized – in waste incineration plants and, in large part, in cement plants, where the tires replace coal as fuel and thus improve the CO2 balance.
Focus on pollutants
To assess health risks from rubber additives in road asphalt, chemists from Empa's Advanced Analytical Technologies lab took a close look at components with risk potential. The results of leaching tests simulating the effects of a rainstorm showed that the levels of polycyclic aromatic hydrocarbons (PAHs), which can cause cancer, are lower in rubber than in asphalt. For heavy metals, zinc served as the lead element; very little of it was washed out. Lead and other harmful heavy metals were present only in harmless traces.
The Empa team also found that harmful benzothiazoles, which accelerate vulcanization in tire production, were released into the environment quickly and in relatively high doses. The experts' advice: remove these compounds before installing the rubber particles, for example by washing them out with water, which can then be disposed of properly.
A benefit for the climate?
Empa researcher Zhengyin Piao is investigating the environmental impact of using old tires in road pavements as part of his PhD thesis in cooperation with the Institute of Environmental Engineering at ETH Zurich. Piao analyzed the entire life cycle of two whispering pavements with rubber asphalt. His calculations based on a model of a one-kilometer stretch of road show that these pavements perform similarly to polymer bitumen asphalt in terms of energy consumption. But they produce significantly lower CO2 emissions – mainly because of the polymers in the conventional product.
So would rubber granules in roads contribute to climate protection? Piao's answer: It depends. In Switzerland, cement plants save so much CO2 emissions by burning old tires that, overall, asphalt with rubber performs a little weaker than with polymers. But if cement plants succeed, as planned, in reducing their CO2 emissions even further in the coming years or even partially neutralizing them with carbon capture technologies, including underground storage, the cards would be reshuffled – possibly in favor of rubber asphalt ...
Whether the idea will catch on in Switzerland depends, of course, on the market. They do have one advantage, says expert Samuel Probst from manufacturer Weibel AG: At least for the moment, they are cheaper than polymer bitumen asphalts. Nevertheless, he remains cautious: "If the test sections develop positively in the long term," he says, "I could imagine that a market will develop for it one day."
Audio |
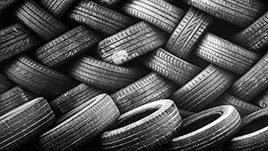
The radio report highlights the research around the new type of rubber asphalt. Radio programme on SRF, Wissenschaftsmagazin, of May 22, 2021 (in German)
Audio |
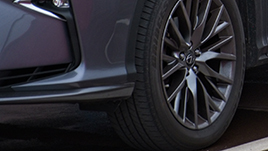
The article explains how used tires are mixed with asphalt in the Empa research project. Radio program on RTS, CQFD, of May 22, 2021 (in French)
Video |
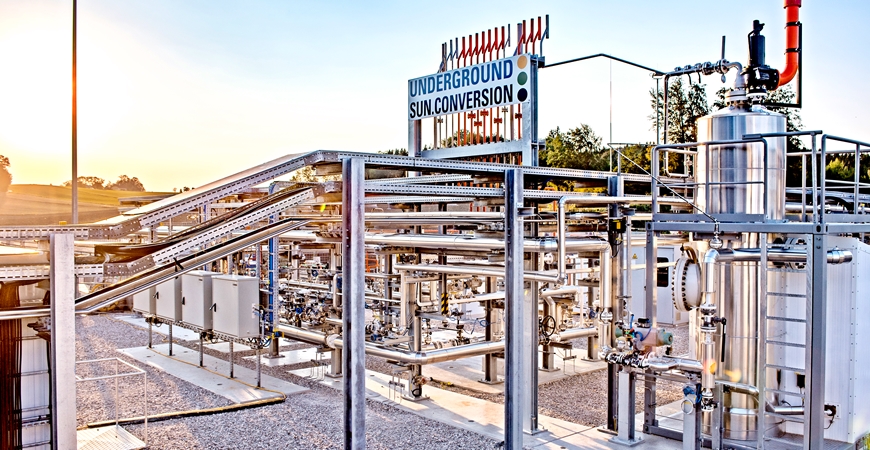
Energy storage
Solar energy from the deep
During the winter months, renewable energy is in short supply throughout Europe. An international project is now considering an unconventional solution: Renewable hydrogen and carbon dioxide are pumped into the ground together, where naturally occurring microorganisms convert the two substances into methane, the main component of natural gas.
>>>>
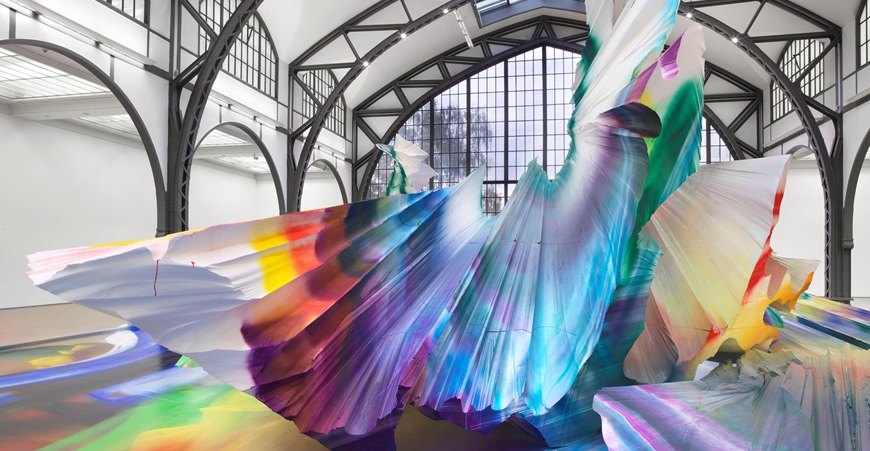
Optics
Molecules in collective ecstasy
When fluorescent dye molecules nestle perfectly together, something completely new is created: an excited state distributed over many molecules. Such collective excitations can be used in a variety of ways – for organic solar panels, in sensors, for ultrafast data transmission or in microscopy, for example. Empa researchers, together with colleagues from ETH Zurich, EPFL, the Paul Scherrer Institute (PSI) and IBM Research Zurich, have succeeded in making such chemical light amplifiers ten times more efficient than before.
>>>>

Chemical contamination
Detoxifiers from the landfill
Bacteria from an Indian landfill could help eliminate contaminated chemicals. The focus is on pesticides such as lindane or brominated flame retardants, which accumulate in nature and in food chains. Researchers at Empa and Eawag used these bacteria to generate enzymes that can break down these dangerous chemicals.
>>>>