From lab to market
Signed by fungi
Local and yet exclusive, natural and yet high-tech: Spalted wood combines contradictions. This very special wood is characterized by patterns of fine black lines, which it owes to a fungus. What used to be a rare chance find in the forest is now a standardized manufacturing process – thanks to the collaboration between Koster AG Holzwelten and Empa.
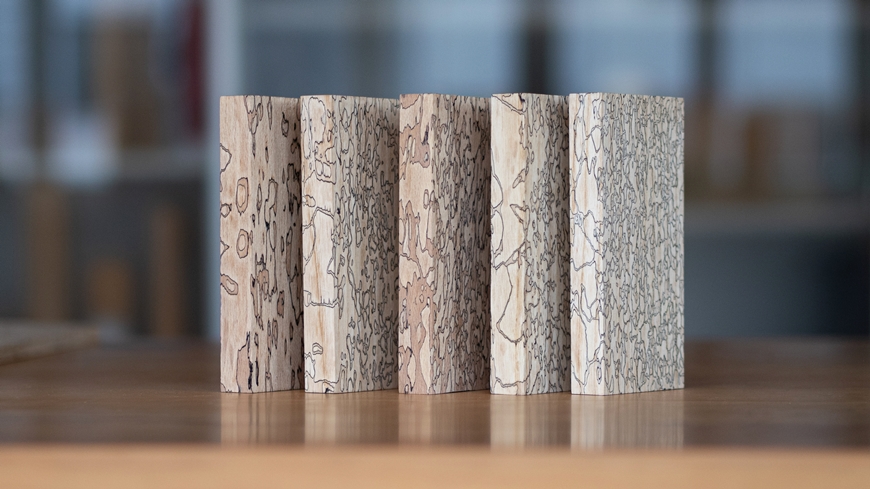
What do you expect from a woodworking business? Precise work and beautiful products, perhaps furniture or a fine parquet floor. Large machines, but also a good deal of manual craftsmanship. Koster Holzwelten, a family business in Arnegg near St. Gallen, offers all of this. In an outbuilding, however, the company shows a completely different, rather unexpected side. Here, in a time-honored, listed building, there are stainless steel containers, laboratories and climate and vacuum chambers. Sterility is a top priority here, and both humidity and temperature are strictly controlled. This is where a unique product is born: spalted wood, which the company developed in collaboration with Empa.
It all started with a few wavy black lines that Jakob Koster, CEO at the time, discovered on a piece of wood from his workshop. Koster showed the piece to Empa researcher Francis Schwarze. The expert in fungi immediately recognized the drawing as a trace of a sac fungus. This inconspicuous fungus is primarily known as a hard-to-detect pest on deciduous trees. However, due to its ability to produce the dark pigment melanin, it has also always been known as a wood refiner. "In the past, tree trunks were left in the forest for several months in the hope that they would be colonized by the right fungus," says Schwarze. That wasn't good enough for Jakob Koster. What if we could produce the coveted spalted wood in a controlled manner, the entrepreneur asked himself?
The idea turned into an Innosuisse project. Together, Koster AG Holzwelten and Empa developed a standardized, scalable process for the production of spalted wood. "I would never have thought that we as an SME could develop something so innovative with a research institute like Empa," says Koster. The great commitment on both sides has borne fruit: Now, around seven years later, the unique product is on the market.
A controlled infection
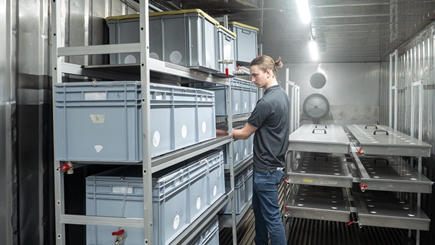
Nothing is left to chance in the production of spalted wood. The boards, which can be up to two and a half meters long, are brought to the correct humidity in a vacuum chamber, sterilized and inoculated with the fungus. They then spend several weeks in a climate chamber while the fungus etches its markings into the wood. With the know-how gained during the project in the Empa laboratories, Koster AG Holzwelten can control and refine the appearance of the melanin pattern.
Once the fungus has completed its work, the wood undergoes a technical drying process, which simultaneously kills the fungus. "The special thing about this particular fungus is that it does not break down the heavily lignified areas of the cell wall; the wood thus retains a high degree of flexural strength," explains Schwarze. The resulting spalted wood with its dancing lines is particularly suitable for decorative applications, for example for furniture, interior design, musical instruments and even jewelry. Inquiries are already piling up, reveals Jakob Koster, who has now handed over the management of the company to his son and is devoting himself entirely to sales and innovation.
Numerous hardwood species are suitable for the production of spalted wood. Koster AG Holzwelten relies on native species such as maple, beech, ash, linden and poplar. Today, these types of wood are mainly used for heating, since they are not considered attractive enough for other applications. "Wood is an important CO2 sink – as long as you don't burn it," says Empa researcher Schwarze. Refining locally produced wood is also a sustainable alternative to exotic import timber. "We have to learn to develop innovative products with our local resources in Switzerland," summarizes Koster.
Hard work, inventiveness – and a bit of luck
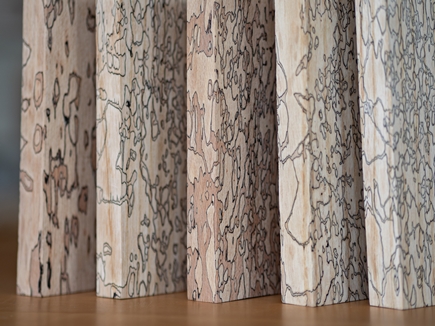
Innovation needs more than just a clever idea: It takes a lot of hard work to turn promising laboratory results into marketable products. No one knows this better than Lewis Douls, who has accompanied the spalted wood project through this transition. The chemist originally came to Empa on a civil service placement. However, he was so enthusiastic about the work in the fungal laboratory that he stayed at the research institute – until he moved to Koster AG Holzwelten two years ago to take over the upscaling of the spalted wood production.
No easy task: Cultivating fungi in a controlled manner is a high-tech undertaking. The conditions that the melanin-producing sac fungus needs to grow are also ideal for countless other types of fungi, and fungal spores are everywhere. "Sterility was the biggest challenge," recalls Douls. Another challenge was cost-effectiveness: A fully equipped biotechnology laboratory does not simply spring up like a mushroom. Expensive equipment, such as autoclaves for sterilization or vacuum chambers for wood humidification, were needed. Here, however, Koster AG Holzwelten was helped by its inventive spirit – and a good dose of luck. The company was able to take over a large part of the climate chambers from a retired mushroom grower. The laboratory equipment came from ETH Zurich, which had commissioned the company with a renovation. What's more, Douls was able to optimize certain process steps, such as the sterilization of the boards, so that a large autoclave was no longer required.
Francis Schwarze is impressed by the effort his project partners have put into the facility. "It's not a matter of course for an SME to acquire so much knowledge and to set up its own laboratory," says the researcher. Schwarze and Douls agree that the company is now even better equipped for cultivating the wood fungus than the Empa laboratory where the project started.
With the challenges overcome, the production line is up and running, and the fungi are doing their decorative work in the air-conditioned chambers. The next step, as Jakob Koster knows, is sales. After the long development period, the new product must become commercially viable. However, the project partners already have new ideas for the future. For now, they are willing to reveal just this: The perfect combination of wood and fungus can do so much more ...
Prof. Dr. Francis W.M.R Schwarze
Empa, Cellulose & Wood Materials
Tel. +41 58 765 7247
Technology transfer
How do innovations get out of the lab and into the wider world? There are different ways, summarized under the term technology transfer. At Empa, technology transfer takes many different forms – be it through direct industry cooperation, Innosuisse-funded projects or by founding start-ups. If these endeavours are ultimately successful, they result in innovative products and solutions that make our world a little bit better.
Read the latest EmpaQuarterly online or download the PDF version.
-
Share
Products with "Empa inside" Technology transfer is a long and complex, sometimes tedious process. Not all research projects lead to a market-ready product – but some do. Here you will find a selection of products in whose development Empa has played a significant role. Some have been on the market for some time, others hit the shelves only recently. What they all have in common: They contain a piece of Empa. |
Research meets industry Innosuisse, the Swiss innovation promotion agency, supports research-based innovation in order to strengthen the competitiveness of the Swiss economy. As part of Innosuisse projects, companies work together with universities or research institutes such as Empa to bring innovative ideas to the market. Empa is currently involved in around 80 running projects of this kind. Here are four of them. |