Empa Research Award 2017
Alloys from the laser printer
In the future, new designer alloys for aerospace applications can be manufactured using the 3-D laser melting process (Additive Manufacturing). Pioneering work in this field was provided by Empa researcher Christoph Kenel, who works today at Northwestern University in Chicago. Empa grants him the Empa Research Award 2017.
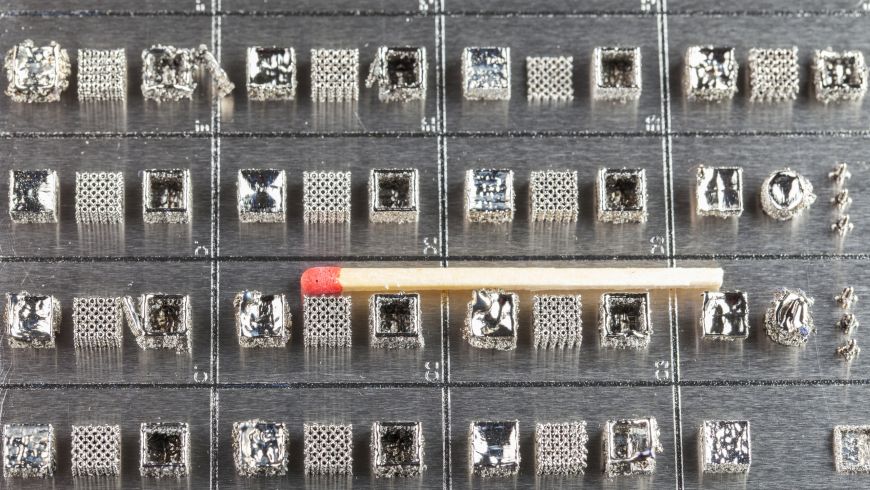
Titan-Aluminum alloys are combining low density, high strength and oxidation resistance at elevated temperatures and are therefore of high technical relevance e.g. in aerospace engineering. The aim of the awarded PhD thesis of Christoph Kenel was to develop a novel titanium aluminide (TiAl) alloy, particularly for use in beam-based additive manufacturing technologies, and to include nano-sized oxide dispersoids to improve their high temperature mechanical properties. Christoph Kenels research was supervised by Christian Leinenbach at Empa’s Advanced Materials Processing laboratory.
The topic is very challenging, since TiAl alloys are inherently brittle at room temperature, and the rapid solidification conditions during AM can lead to complex phase transformation sequences, pronounced element segregation and cracking. Oxide dispersion strengthened (ODS) alloys are a class of materials that offer an unmatched combination of deformation-, creep-, coarsening- oxidation- and corrosion resistance at temperatures up to 1,000 °C.
Alloys not feasible by classical casting
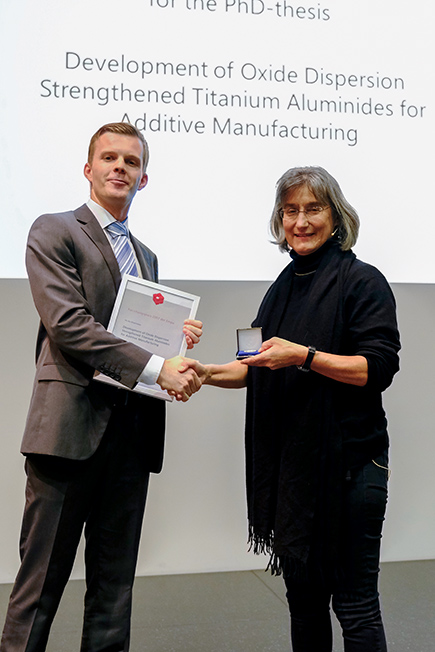
However, the manufacture of components using ODS alloys is currently subject to severe economic and technical barriers. Conventional wisdom is that classical powder metallurgy is the only available method to create ODS alloys from powders to which oxides were added via ball milling in a pure solid-state process: if these composite powders were melted, their oxide dispersoids are lost via one or more of coarsening, dissolution, agglomeration into interdendritic space and floating to the surface of the ingot (‘slagging”). Processing ODS TiAl is thus a truly demanding task.
Dr. Kenel decided for a novel approach to develop a TiAl alloy specifically for the additive manufacturing (AM) process. In general, the AM processing parameters are optimized for a given material in a trial-and-error manner, but it has been known that this approach often fails. Considering the oxide dispersoids, Kenel and his colleagues hypothesized that laser-based AM can be used successfully to create bulk samples from oxide dispersoid-containing powders, as the very short melting time and very rapid solidification would keep the oxide dispersoids well dispersed within the alloy grains.
In his work, Dr. Kenel used computational methods (computational thermodynamics, finite element methods) for simulating the phase transformations in binary Ti-Al and ternary Ti-Al-Nb and Ti-Al-Mo alloys, respectively, during the very special heating and cooling conditions during AM. He then developed sophisticated new experiments including in situ synchrotron X-ray micro diffraction methods during laser heating, allowing him to systematically study the phase and microstructure formation in selected alloys under well-defined and simulated AM conditions with an unprecedented temporal resolution. This has not been done before.
The Research Award 2017 was awarded on November 13 on the occasion of the "PhD Day" at Empa. Christoph Kenel traveled from Northwestern University in Chicago, where he has been conducting research since the beginning of the year.
-
Share