Swissloop and Swissloop tunneling
Las Vegas breakthrough
Ultra-fast capsules in vacuum tubes: All around the world, companies and research institutes are working on "Hyperloop" concepts. Swissloop Tunneling, a student initiative, is developing a drilling machine for underground transport tubes. The first reward for their efforts: a second place in an international competition in Las Vegas.
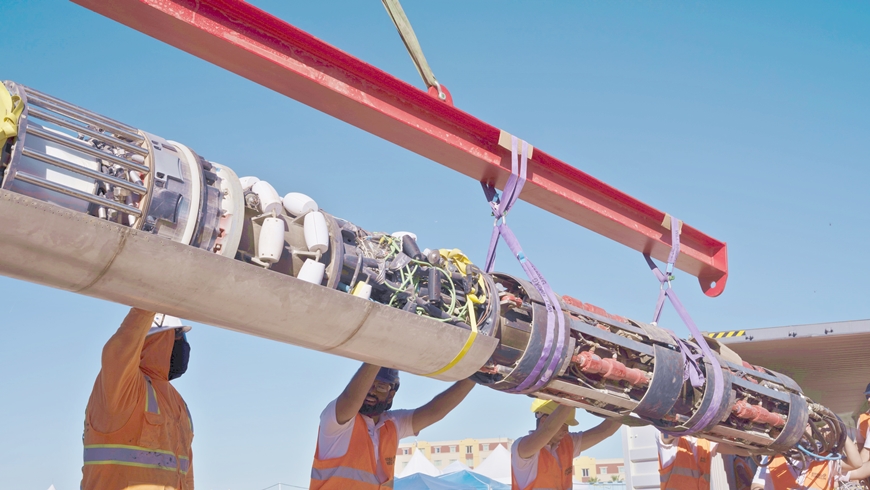
400 student teams from all over the world had applied; only a dozen qualified last September for the "Not-A-Boring-Competition" in Las Vegas, the tunneling competition that entrepreneur and Hyperloop promoter Elon Musk had launched. Inspections by a jury of experts on the Groundhog Alpha drilling rig lasted for days (see infobox); then the Swissloop Tunneling team from ETH Zurich and other Swiss universities qualified for the final: the attempt to drill a 30-meter-long tunnel with a diameter of 50 centimeters. An endurance test for people and material, as Eugenio Valli and Lukas Heller from Swissloop Tunneling can tell.
Hyperloop routes appear to many contemporaries to be a distant future or even science fiction, but work on them has long been underway in many places – and not just at universities such as ETH Zurich or EPFL. Companies like Virgin Hyperloop in the U.S. and others have long been investing in this technology, although many technical questions remain unanswered. The most important argument is environmental protection: Floating in a vacuum tube could drastically reduce energy consumption and CO2 emissions.
While Groundhog Alpha is still on its way back to Dübendorf by sea, the team is starting to prepare for the coming year – with about 30 new students joining. One focus will be on the particularly important parts of the machine. For example, on the "liner" segment, which 3D prints the tunnel wall as it is being driven, using polymers that in turn encase tear-resistant fiberglass foils. Designers want to rework this novel technology to make it work reliably.
Groundhog Alpha – an innovative tunnel drilling machine
Mr. Valli, Mr. Heller, second place in Las Vegas – was that a victory or a defeat?
Lukas Heller: For us it was a huge victory! Although eventually we couldn't dig into the ground at all with our drill in the final ...
Why was that?
Heller: There were many factors. A storm in the desert damaged the drill: There was damage to various systems, especially the electronics due to lightning and rain. We also had error messages that we couldn't fix in time: When we were about to be able to start, the deadline had just passed.
Eugenio Valli: But we were one of only two teams to get permission to start at all ...
Heller: ... and we achieved what we aimed for. We wanted to innovate – and we won the prize for the most innovative system and for the best design.
It was the first competition of its kind. What do you take away for the future?
Valli: At the beginning, you imagine it's almost too easy to drill a tunnel. But the more experience you gain, the clearer potential problems become. For this year, we have therefore concluded: We're going to do much, much, much more testing!
Heller: We learned an enormous amount. Our motivation now is to be able to improve a few things as a result.
Many tasks still to be solved. Are real drilling tests already on your schedule?
Heller: We had already considered doing a test on Empa's construction site here in Dübendorf in the summer before the competition. But then it rained heavily; that was too risky for us. But in spring it must happen, and it will; the only question is: where.
Young experts interviewed
According to your website, you not only have Hyperloop tunnels in your sights, but also conventional tunneling. Instead of half a meter in diameter, far larger scales – quite a bold vision ...
Heller: Exactly. But at the moment, what's most important to us is that we innovate. In future, we could perhaps work with manufacturers to initially scale up individual systems of our Groundhog Alpha for machines that already exist.
Valli: The costs and necessary infrastructure would then also become much greater.
But you are sticking to this ambition?
Heller: Definitely! (Both laugh.)
You were recently at an important technology trade fair, Gitex, in Dubai to present your concept. What were the reactions?
Valli: Many people are fascinated by Hyperloop technology, especially the high speeds of up to 1200 kilometers per hour. And a connection between Dubai and Abu Dhabi: There is a lot of interest in that region.
Heller: Something is also happening in Switzerland. SBB is cooperating with our new partner Eurotube, which is developing vacuum tubes, for a test tube in Collombey-Muraz in the canton of Valais.
You have recently formed an alliance with Eurotube and Swissloop to speed up the Hyperloop concept. What are you planning spcifically?
Heller: For our "lining" system, i.e. the tunnel shell with 3D printing, Eurotube will help us with expert advisors, because our work does touch on this point. Eurotube already supported our team a lot with selecting the materials for the polymers for printing.
You also get support from companies. How many partners do you have thus far?
Valli: About 80. Some support us financially; others mainly contribute knowhow. Or even manufacture systems for us, like the unique control mechanism from the Hagenbuch company in Ebikon. Six movable hydraulic cylinders that allow the machine to move freely at the front or even retract the drill head – for example, when it hits an obstacle in the ground.
Could you have done that without partners?
Valli: No, not in this short time. Something like this is really a big help!
Heller: And you shouldn't forget Empa as a founding partner. Our working space on campus is priceless, with the crane in the workshop and so forth. The drilling machine weighs two and a half tons – without that: no chance!
Valli: Empa is home for us.
And how do you look to the future after the first year?
Heller: We have two goals. Of course, the exciting vision, the technology and the innovation. But just as close to our hearts is getting the brilliant minds at ETH Zurich out of the lecture halls and giving them an opportunity to work hands-on, so they can manufacture something from A to Z.
The "Simon Ammann Pod"
In mid-July, students from ETH Zurich traveled to Valencia with their latest pod, developed at Empa, and discussed a possible implementation of the Hyperloop concept with researchers and industry representatives.
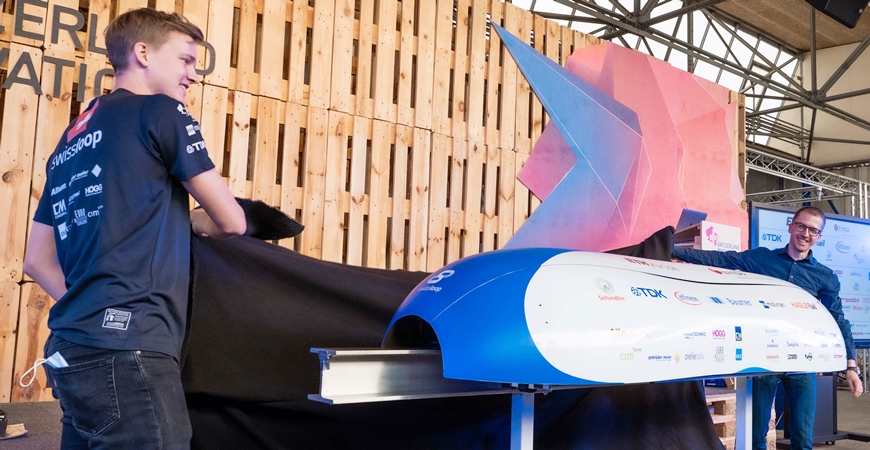
In 2013, Tesla and SpaceX founder Elon Musk presented his Hyperloop concept for the first time. Since then, student teams from all over the world have competed in annual Hyperloop Pod Competitions to develop high-speed vehicles – so-called pods – for travel in vacuum tubes. Successful participants included teams from ETH Zurich, which took part every year until 2019 with new prototypes. In the Corona year of 2020, the event was cancelled, and in 2021 the "Not-A-Boring Competition" was held for the first time instead. Nevertheless, Swissloop continues to dedicate itself to vehicle development. In mid-2021, the ETH Zurich team unveiled its latest prototype. True to its namesake "Simon Ammann", four-time Olympic champion in ski jumping, the pod has the ability to hover – and can thus greatly reduce friction losses. However, unlike in previous years, the team did not travel to California with it, but competed with other European teams at the European Hyperloop Week in Valencia – with great success: The expert jury rewarded Swissloop with four out of five technical awards. The team is currently working on a new prototype for 2022, when the next competition will be held in Delft.
Stephan Kälin
ETH Zürich student team Swisslooptunneling
Swissloop team from several Swiss universities
-
Share